Which Manufacturing Process Should I Use?
Deciding what materials make sense for your project
An important part of beginning the development of a product is knowing what materials are practical for the ultimate use and demographic of your product. Selecting materials and processes that are too expensive or too fragile can ruin the profitability of a product and hurt the reputation of a company. Therefore, before anything evolves beyond a napkin sketch, you should answer some questions and identify what materials will handle the job.
Answering these questions allows you to begin to understand what you value in your product and will act as a starting point for design since all manufacturing processes have different limitations and setup/production costs.
- Will this be a low production (1-100) or high production (up to millions+) product?
- Does the product need strong aesthetic design?
- Will the product undergo heavy structural stress?
- If the product fails, could it potentially be dangerous?
- Is the product targeting an especially low or high end consumer?
- Is the product disposable so that recycling is an issue?
- Are there certain properties like waterproofing, magnetism, electrical conductivity, etc. that the product must or cannot have?
Answering these questions allows you to begin to understand what you value in your product and will act as a starting point for design since all manufacturing processes have different limitations and setup/production costs.
Metalworking Processes
Metalworking processes are typically used for low volume/high quality applications where strength is important. Depending on how the metal is formed, the strength, rigidity (elastic modulus), and fracture-resistance (toughness) will vary greatly.
Machined Metal
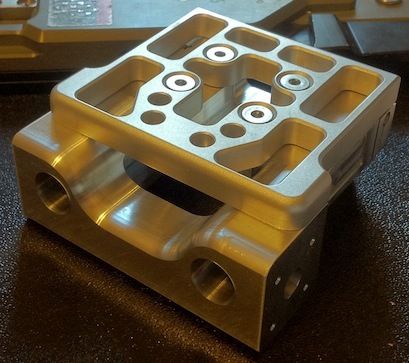
In recent years, thanks to direct interaction with computer drafting/modeling software, CNC machined metal has become the method of choice for most low-production products. Machined metal generally offers the best possible mechanical properties for a given material (aluminum, steel, stainless steel, etc.) because it starts with a uniformly extruded material blank. To create a part, the metal extrusion is secured to a mill or lathe machine and then material is cut away by the machine with special tools until the part is complete.
Advantages:
Disadvantages:
What products should use this?
Advantages:
- Quick setup compared to most processes
- Low initial cost
- Excellent material properties and coincides well with engineering calculations
Disadvantages:
- Parts get more expensive as you remove more material
- Doesn't work well for highly stylized parts
- Pocket depth is often limited and requires careful design consideration
- Requires post-processing if tool marks are not acceptable
- Among the highest per-part costs for a manufacturing process
What products should use this?
- Products that require high and predictable strength characteristics
- Very low production products
Cast Metal
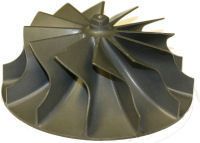
Cast metal is one of the oldest forms of metal forming. Casting is performed by heating metal to a molten state and then pouring it into a pre-formed mold. There are many types of metal casting based on the quantity and quality desired.
Advantages:
Disadvantages:
What products should use this?
image credit: MarkBolton at en.wikipedia
Advantages:
- Allows for the most design freedom of the traditional metal working processes
- Often produces the lowest per-part cost for metal
- Usually provides the best finish for a metal part without post-processing
Disadvantages:
- Somewhat unpredictable mechanical properties due to air bubbles and varying temperatures during the molding process
- Either has high setup cost or high per-part cost depending on the specific casting process
- Usually somewhat brittle compared to other metal processes
What products should use this?
- Products that need reasonably high strength, but not as much as machined metal
- Products with higher production than is practical for machining
- Products that must be metal but can't be formed by other traditional processes
image credit: MarkBolton at en.wikipedia
Sheet Metal
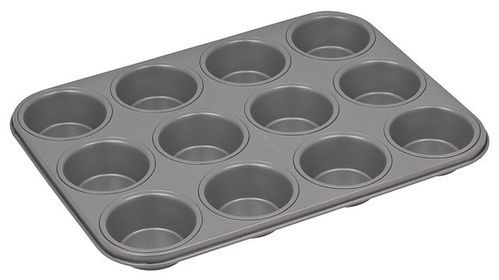
Sheet metal is commonly used for large, hollow containers or for fairings/covers for large products. A few good examples of sheet metal use would be a stainless steel trash can, the outer shell of a washing machine, or the body panel of a car. Sheet metal is rarely the only process used to construct a product, but can be used to inexpensively create aesthetically-pleasing covers and some very specially designed mechanical parts.
Advantages:
Disadvantages:
What products should use this?
Advantages:
- Allows you to cover a large surface area with the lowest cost
- Can sometimes be cleverly constructed to make exceedingly low cost products compared to other metal processes
Disadvantages:
- Requires careful ribbing or folding to have structural rigidity
- Often prone to dents and dings due to thinness and ductility
What products should use this?
- Products requiring large, thin enclosures
- Products that fit within the stringent capabilities of structural sheet metal
Plastic Processes
Injection Molding
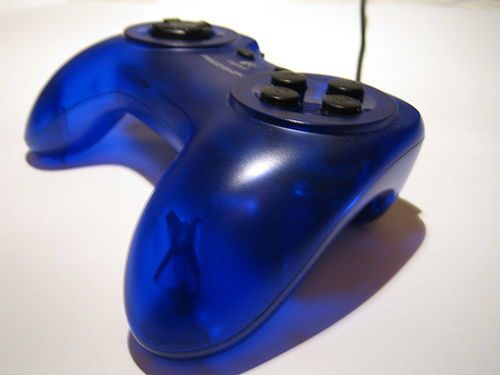
Injection molded plastic has been the cornerstone of modern consumer product manufacturing and industrial design since the 1940s when the modern screw-type injection machine was invented. Injection molded plastic benefits from extremely low per-unit costs and allows for a wide variety of designs to made quickly and easily.
Advantages:
Disadvantages:
What products should use this?
Advantages:
- Low per-unit costs
- High design flexibility
Disadvantages:
- Parts generally have to be thin and have a uniform thickness throughout
- Must be a parting line in the finished part and must be designed with draft (taper) to be easy to eject from a mold
- Setup costs make this process uneconomical for low production runs
What products should use this?
- Mass produced products
- Intricate designs
- Products that must have a low per-unit cost
Blow Molding
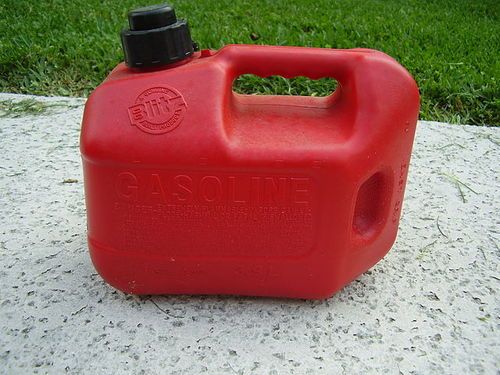
Blow molding is most commonly used for liquid containers. This process can also be used for making large shapes that would be too costly to make in another process and doesn't have high strength requirements.
Advantages:
Disadvantages:
What products should use this?
Advantages:
- Low per-unit costs
- Large size for relatively small cost
Disadvantages:
- Low strength
- Somewhat high setup cost
What products should use this?
- Mass produced products
- Products that must have a low per-unit cost
- Products designed for liquids.
3D Printing
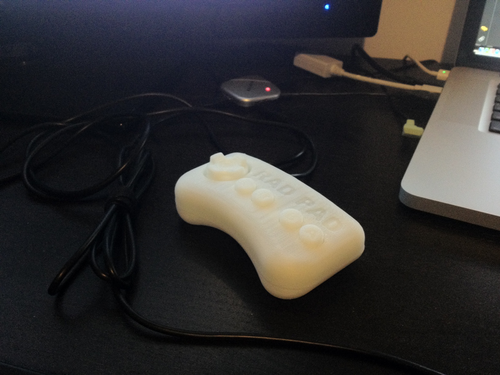
The newest of manufacturing techniques and by far the most flexible. Traditionally used solely for prototyping, the rapidly declining costs of 3D printing makes it viable for low-production products or products that require extreme geometry that isn't practical for other processes.
Advantages:
Disadvantages:
What products should use this?
Advantages:
- No tooling cost
- Extremely versatile
- Requires significantly fewer design hours to create
- The only choice for "need it yesterday" one-off situations
Disadvantages:
- Among the highest per-part cost
- Slow cycle time per part (hours instead of seconds/minutes)
What products should use this?
- Prototypes
- Extremely low-production products
- Products that require forms that traditional processes can't make